Jenga 3000: Tower Builder
- Timothy Bukowski
- May 1, 2020
- 3 min read
Updated: May 4, 2020
April 2020
Overview
For this project I worked with a team of four to design a 2.5 degree of freedom machine that would build a Jenga tower. This machine had three main components: a rotating base, a lifting platform, and a pushing mechanism. The half degree of freedom was from the actuating mechanism which placed the blocks on the tower. The rotating base along with the lifting platform provided movement with two degrees of freedom, together allowing it to place the layers of Jenga blocks in alternating position as it builds the tower up. The blocks were placed by a pushing mechanism with was the other half degree of freedom.

Objectives
Synchronize multiple parts to work together and create a fluid machine
Create a mechanism to follow a desired path
Become familiar with Solidworks Motion Simulation
Design
Dispensing Mechanism
As you can in many of the sketches, at first a conveyor belt pulling from a hopper seemed like the best way to dispense the blocks. However, we later worried that the blocks would get stuck in coming from the hopper, so we switched to a layout that would instead have the blocks stacked. It would then be able to just push out the bottom layer to dispense them onto the tower. This push motion was created by a simple mechanism.
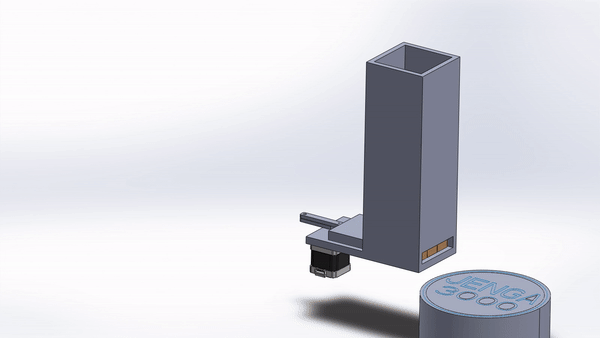
The motion of the mechanism is driven mostly by the arm connected to the motor shaft. The length of this are is half of the distance that the pushing block will move, which we made to be a little longer than the Jenga block. The swinging arm along with the pushing block can be used to position where the motion takes place
2-D Movement System
Our 2D movement consisted of a rotation along with a lift. We thought of using gears for both movement directions, however for the Z movement we found that spinning a screw to move a platform upwards made much more sense and allowed for a lower tolerance. To rotate the system we used a spur gear which ran inside of a stationary base internal ring.
Features:
Stepper Motors to drive motion
Platform to hold Jenga tower
Screws to drive dispenser up and down
Gear set to rotate the machine around internal gear base
Final Assembly and Simulation
We ran into quite a few problems when we ran the simulation which took quite a while to debug. First we found that we could only have one level of subassembly, which made organization of the CAD a bit more messy that we would have liked. We also found out that while the dispenser demonstration could treat the blocks as individuals, unfortunately in the final assembly we were limited to grouping the blocks into each layer. We controlled the movement by choreographing the rotation of each motor to make the system move smoothly.
Conclusion
In the end the project was a success all around. We were able to create a model that could build a Jenga tower and I was successful in completing all of my objectives. I learned how to make a mechanism to do a desired repetitive task. I was also able to synchronize to two motions systems to work together to create 2D movement. I really enjoyed learning to use the motion simulation in Solidworks and learning its features as well as its drawbacks.
There is also a lot that I would change about our design in the future if we were to build it. We would likely run into many features getting locked up due to friction. We tried to avoid this by putting dispenser as close to the screw and support rod, however we would likely have to increase the size of the collar on the screw or add counterweight to the opposite side of the platform. I would also make aesthetic changes to make it a more appealing product such as add a case to cover the entire machine.
Comments